Nyrstar Budel in the Netherlands was recently in ‘care & maintenance’ mode for several months in response to external factors impacting the business, with a temporary production stop to allow maintenance to be conducted. However, this did not mean that employees were twiddling their thumbs. ‘Among other things, we used this period to provide employees with further training’, says HR manager Jinny Kurvers.
‘I don't believe it ever happened before in Budel's 130-year history that the plant went into 'care & maintenance' mode due to external factors', says Jinny Kurvers.
In terms of training, Nyrstar has a reputation to uphold. ‘Although our in-house school works closely with an external school, we also give courses ourselves. A lot of training is also done on the job by mentors.’
In the past few months, the focus was on technical training, though the intention is to further develop people skills as well. ‘About 75 percent of leadership roles are filled internally’, says Jinny Kurvers. ‘To ensure that employees are prepared for a leadership role when the time comes, we work hard on developing their leadership skills well in advance.’
Retaining and nurturing talents and safeguarding know-how are always a key concern for us.
Jinny Kurvers,
HR Manager at Nyrstar Budel
Motivation
While a period like the one in Budel is primarily a technical challenge, Jinny Kurvers also has an eye for the human impact. ‘Keeping our people motivated during that uncertain period was a top priority. Especially as the
labour market is very tight at the moment. Retaining and nurturing talents and safeguarding know-how are always a key concern for us. Though it was no easy task to convince people to come and work for us when the plant was down, this actually worked out quite well.’
Choice
The fact that production in Budel was stopped did not however mean that facilities were unmanned. ‘Each department is manned by at least two to three people. And the shift system just continued. We gave everyone the choice to continue working their shift schedule or temporarily switch to day shift. That was a conscious decision, because people also plan their personal lives around their shift schedules.’
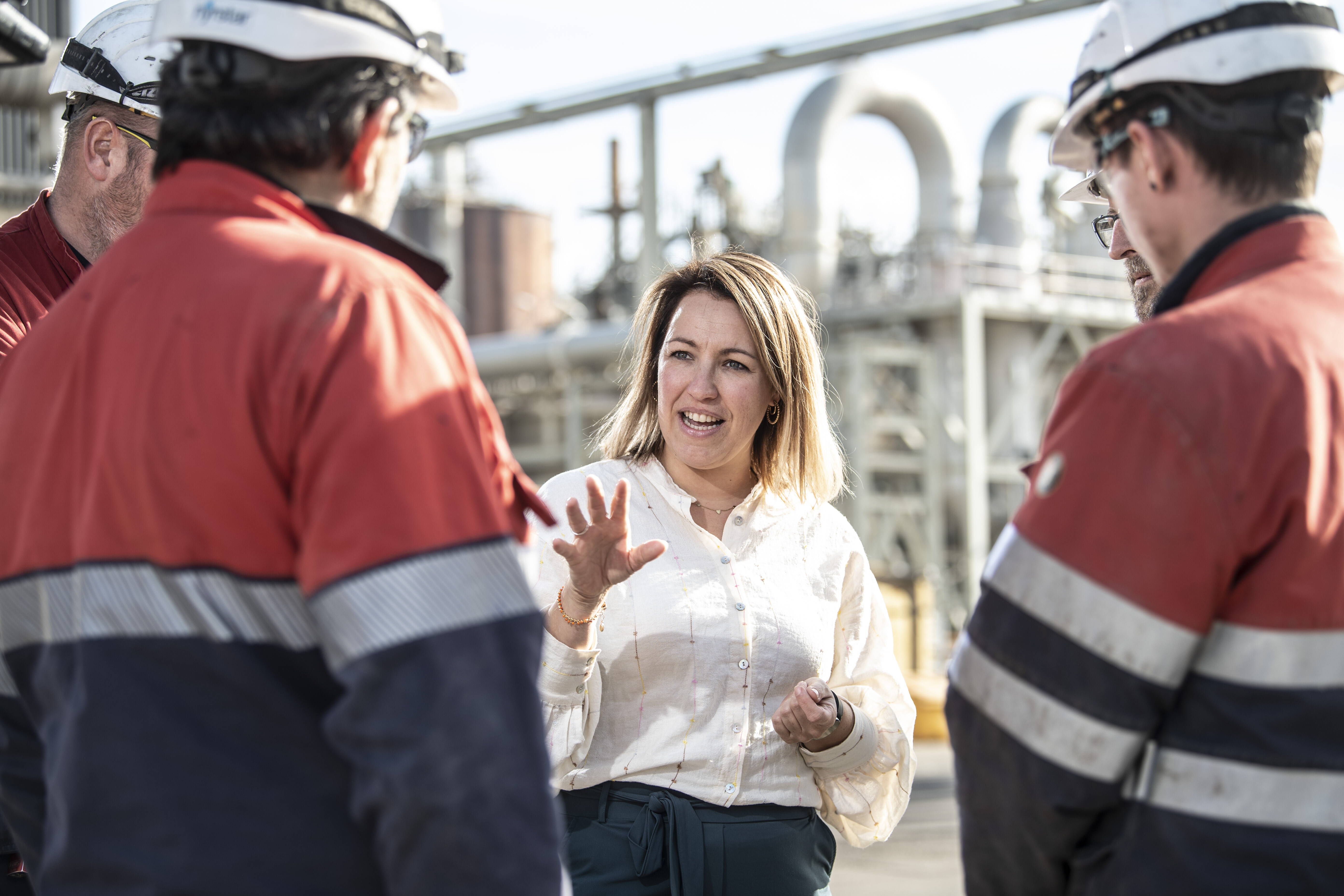
While Nyrstar Budel was in ‘care & maintenance’ mode, facilities in Balen were still operating, albeit sometimes at reduced levels due to the situation on the energy market. ‘What our HR colleagues in Budel did shows how flexible we are. Making a virtue out of necessity, we are continuing to put our people first. In Balen as well. Even though we are having to constantly adjust our production, we are continuing to invest in our people’, says Frederik Heylen, HR manager at Nyrstar Balen.