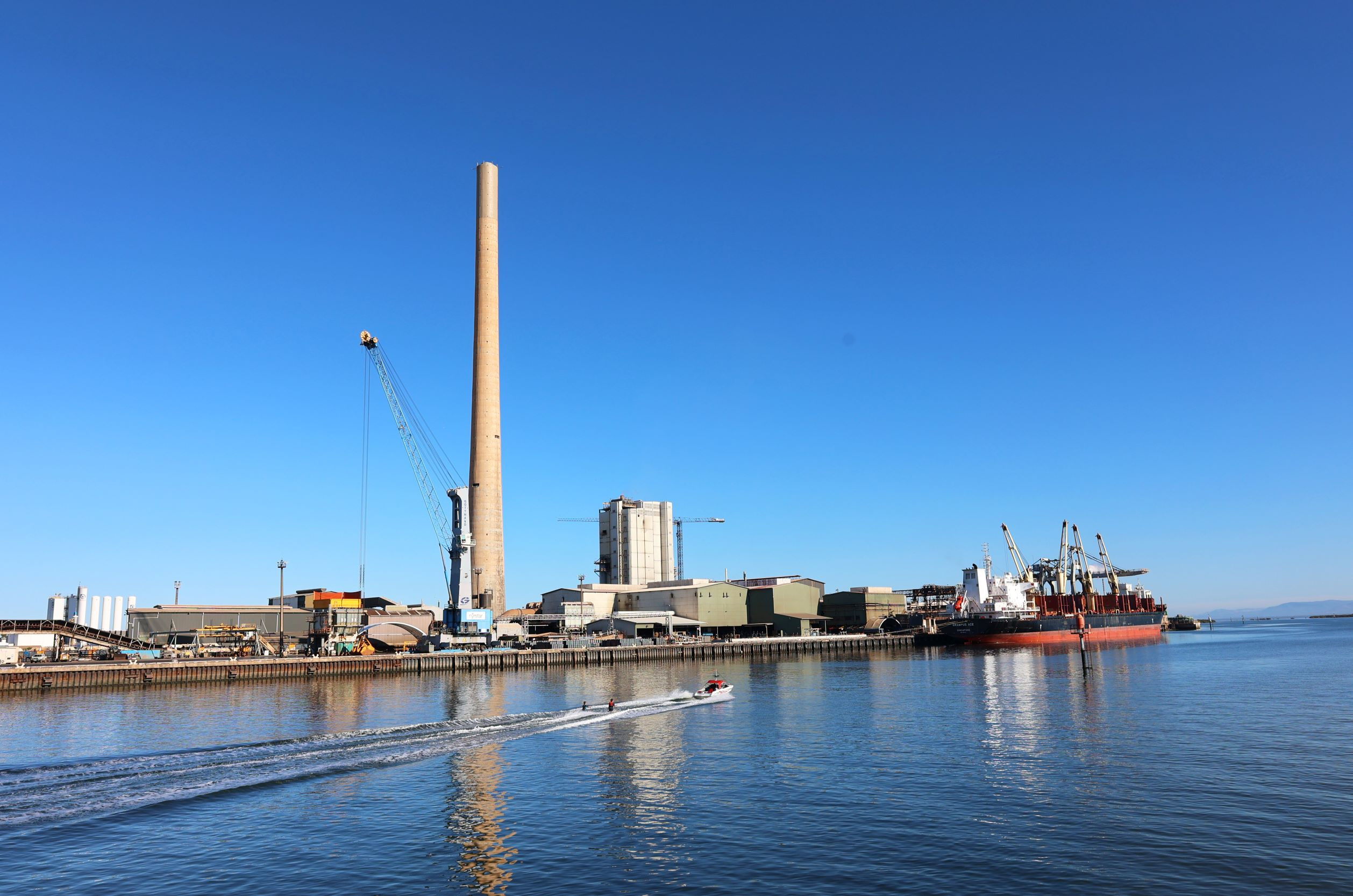
Overview
Nyrstar's Port Pirie multi-metals processing facility has been in continuous operation for more than 130 years, employing over 800 people and 250 contractors. The site is located in the Upper Spencer Gulf, 230 kilometres north of South Australia’s capital city, Adelaide.
The plant is one of the world's largest multi-metals smelters, processing and refining lead, silver, zinc fume, copper matte and by-products such as sulphuric acid - all products that are essential for the renewable energy transition.
There is an adjacent dedicated port facility where concentrates are received, with final products dispatched by road and rail.
To read a summary of our 2024 Economic Value Report and our contribution to the Australian economy. Click here.
Investing in Nyrstar’s safety, environmental and operational improvements
Nyrstar continually invests in environmental projects, including commencing construction of a 6,850 square metre product recycling facility at its Port Pirie plant that will significantly reduce lead-in-air concentrations measured in the local community. The product recycling facility will build upon a range of plant and process improvements that Nyrstar Australia has made in recent years to address the different factors contributing to lead in air concentrations.
The facility will be sealed and under negative air pressure, allowing intermediate materials used in the production process to be stored and mixed in an enclosed facility, thereby reducing the potential for losses of lead-bearing dust from the plant into the atmosphere.
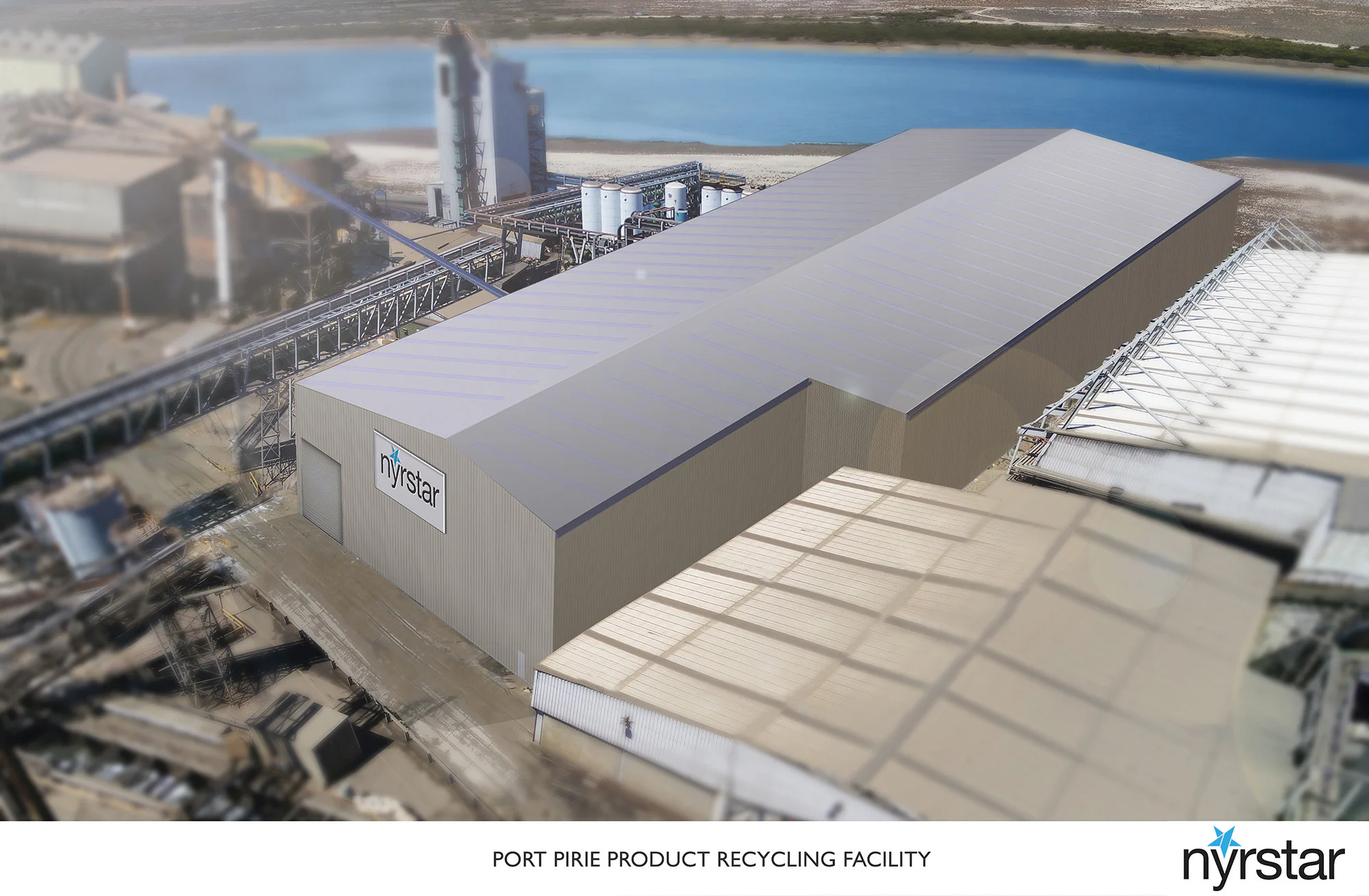
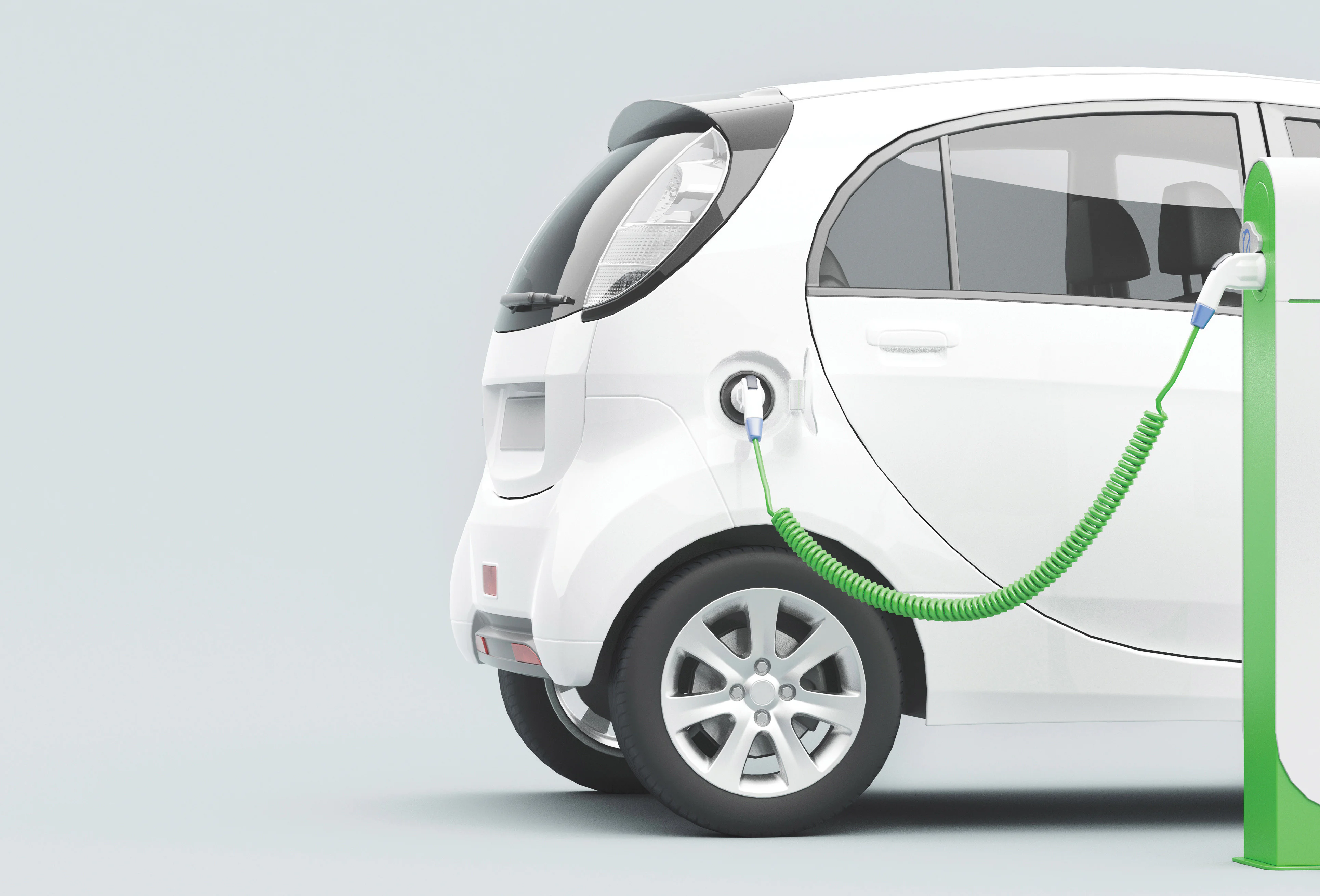
Critical minerals and metals
Nyrstar Port Pirie’s products are essential for the energy transition and a low carbon future.
Lead
Lead is a key component in the production of car batteries, pigments, solders, cable sheathing and radiation protection. It is also required in many sustainable products including hybrid and electric vehicles, photovoltaic panels and renewable energy storage.
Silver
Silver has the highest conductive properties and is vital to the production of photovoltaic cells. The automotive industry uses silver to produce membrane switches used for turning on and off a circuit.
Sulphuric acid
Sulphuric acid is used by the chemical industry in the production of fertiliser, but is also important for mineral processing, oil refining, wastewater processing, and chemical synthesis. The chemical has a wide range of end applications, including domestic acidic drain cleaners, as an electrolyte in lead-acid batteries, in compound dehydration, and in cleaning agents. It is also an essential ingredient in the production of fibres, paint, rubber, plastic, steel and medicine.
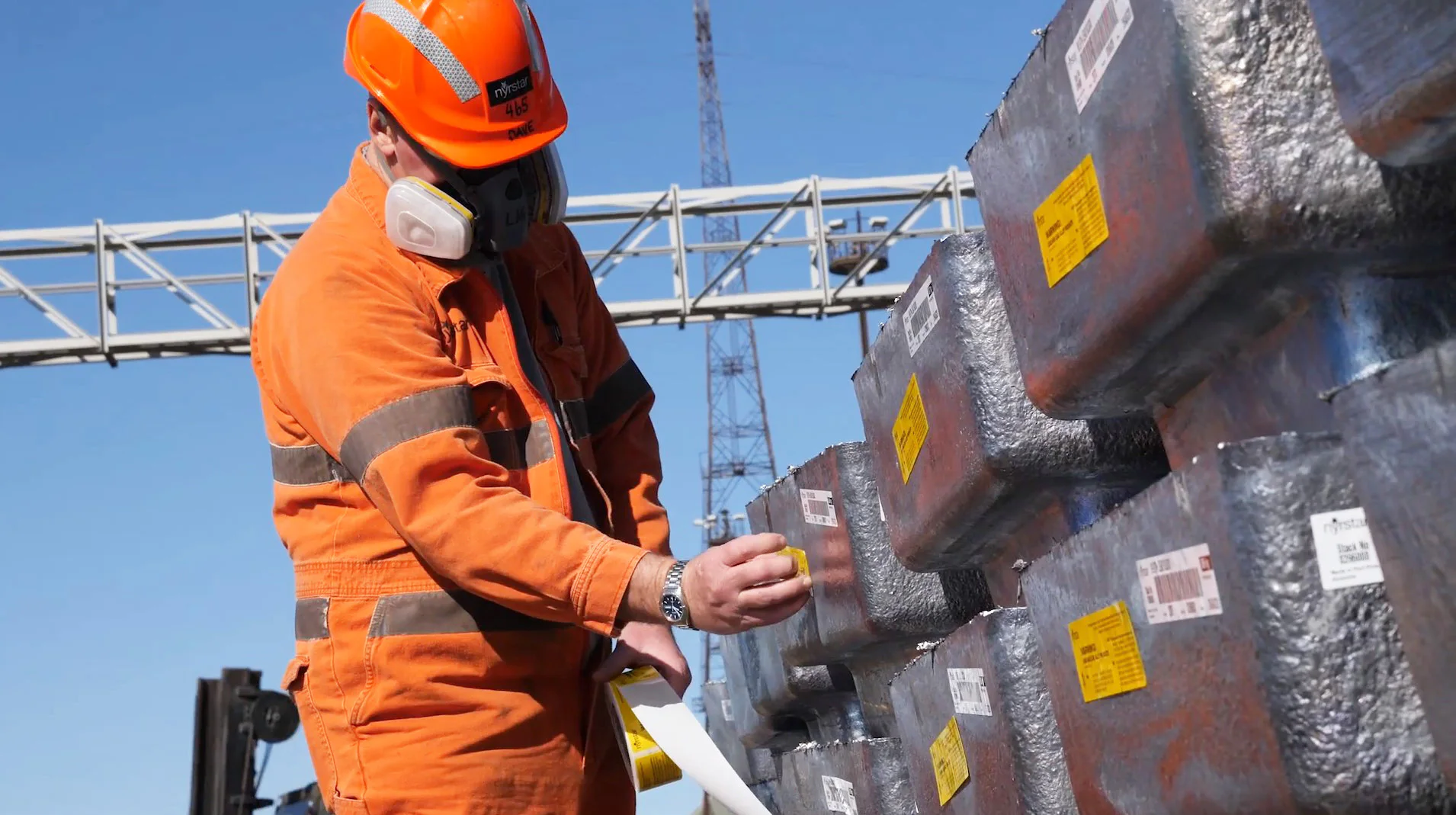
Quick Facts
Technology: top submerged lance (TSL) furnace, blast furnace and lead refinery. Slag fuming leach, solvent extraction/electrowin (SXEW)
Products: commodity grade lead, copper matte, silver dore and sulphuric acid
Employees: ~800
Nyrstar Port Pirie holds certificates for:
History
After over 130 years of continuous operation, the Port Pirie Smelter has a rich and dynamic history. Port Pirie was South Australia’s first provincial city and the fourth declared Port in Australia. Port Pirie is one of the key regional cities in South Australia, with the Port Pirie Smelter being one of the major employers of the Upper Spencer Gulf region.
The first smelting operations commenced at Port Pirie in 1889 and a long history of smelting has followed. The Port Pirie community is extremely parochial about the smelter with generations of the same family often having worked at the facility.
The community and the smelter are intrinsically linked. Nyrstar is committed to reducing its environmental footprint and has a strong focus on reducing emissions from the site. For numerous years the site has worked proactively with key stakeholders developing and implementing community initiatives that reduce exposure and improve community health particularly with young children (www.tlap.com.au).
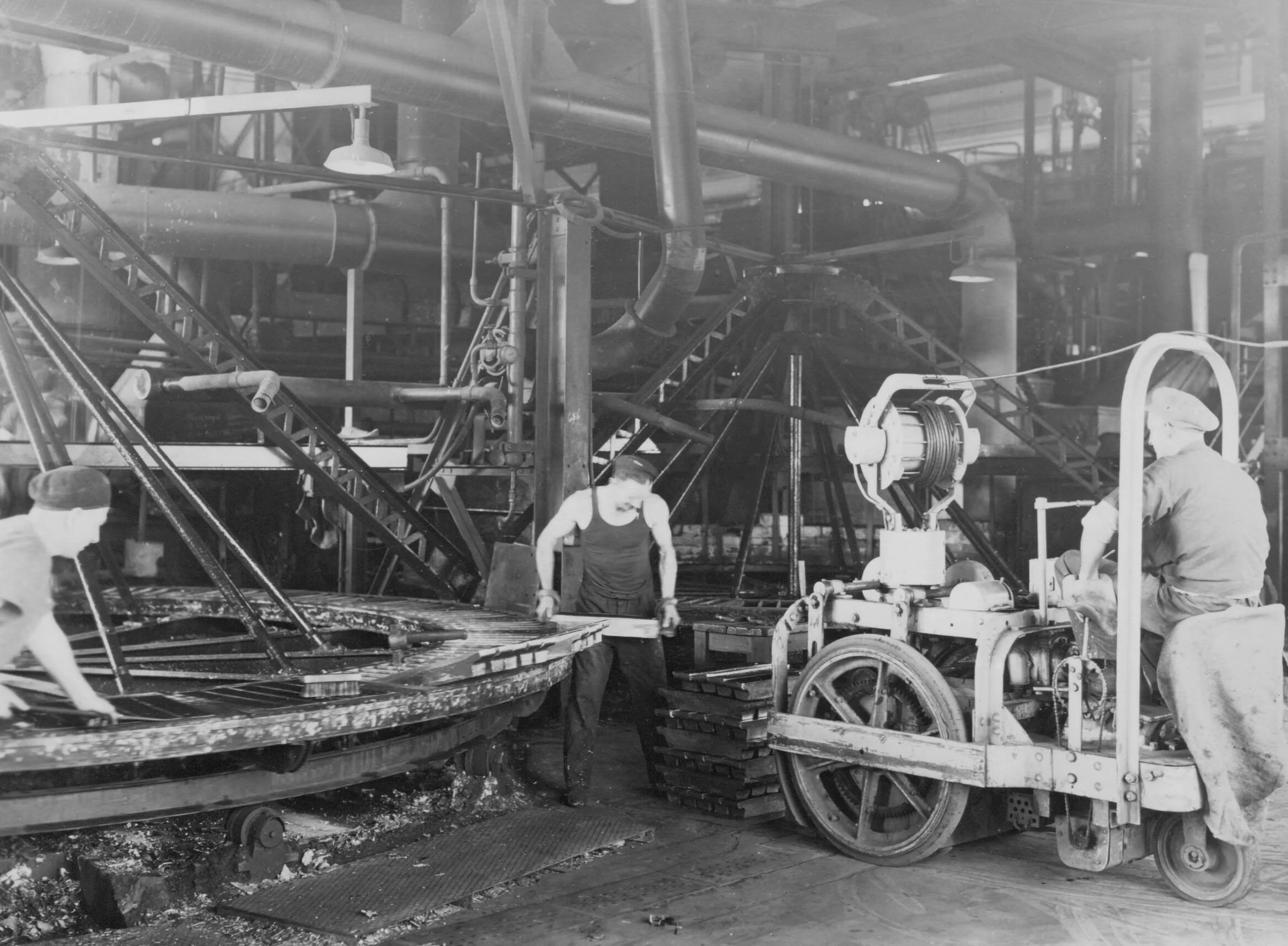
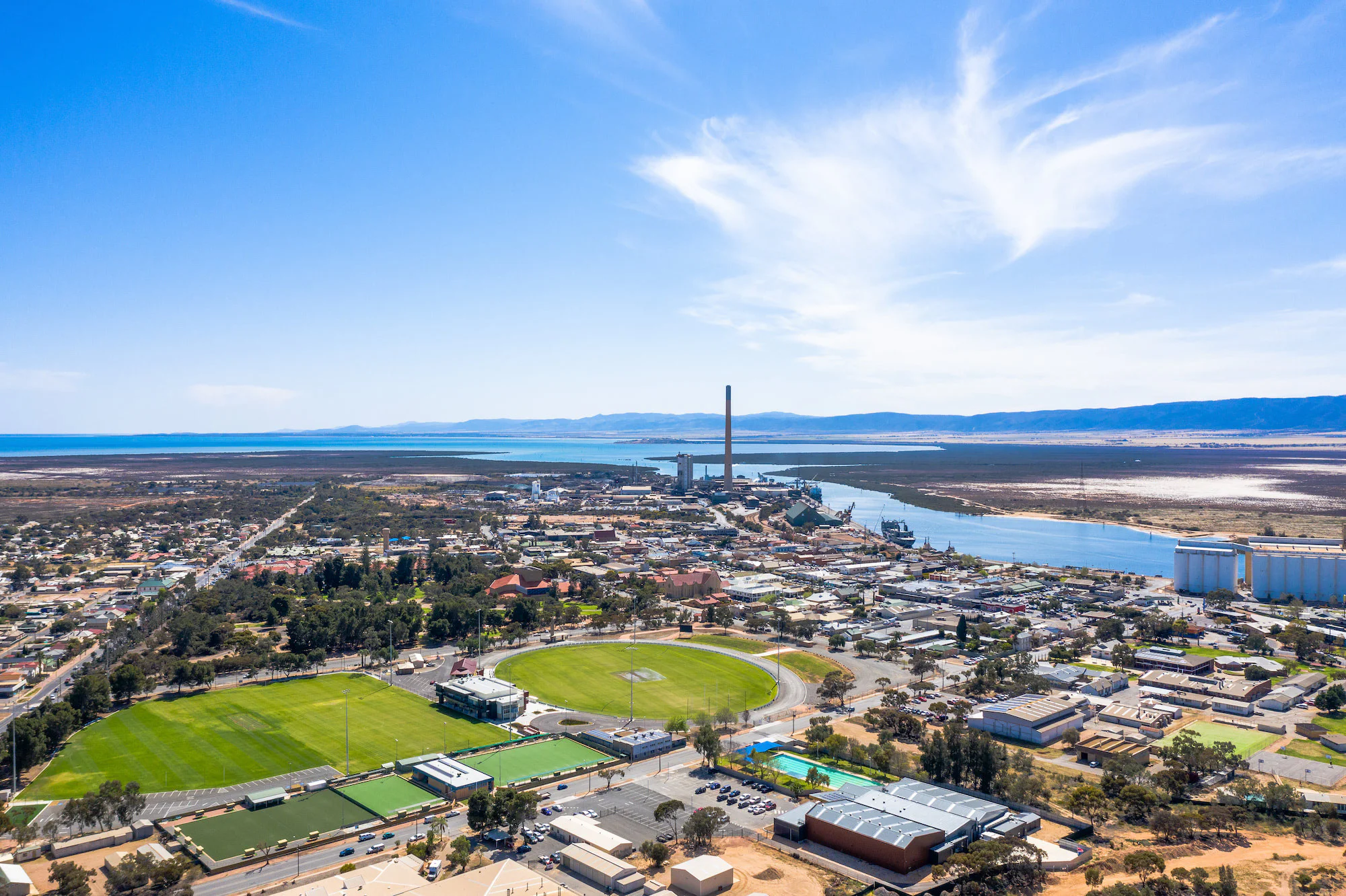
Community Consultation
Nyrstar Port Pirie provides the community with information about our environmental plans and performance consistent with our commitment to transparency through regular ongoing reporting on this website.
Air quality improvement at Nyrstar Port Pirie community information booklet (Updated August 2024)